I wanted to ensure that there is sufficient clearance between the cowl and the plenum across the entire plenum. I came up with the idea of placing blobs of something on top of the plenum and then installing the top cowl. I wanted something that would deform pretty easily so that it wouldn’t deflect the plenum, but stiff enough that it will stand up by itself without sagging. My wife suggested a product called Moon Dough that my son had. This worked perfectly. It deforms with practically zero pressure, but won’t move on it’s on. As you can see, the blobs flattened down nicely and perfectly reveal the clearance at each point. I measured all of these, and they’re all very close to 1/2″. I’m going to trim the baffles down another 1/8″, but the thickness of the plenum and the screw heads will eat up some of the clearance. I should end up with at least 3/8″ all the way around.
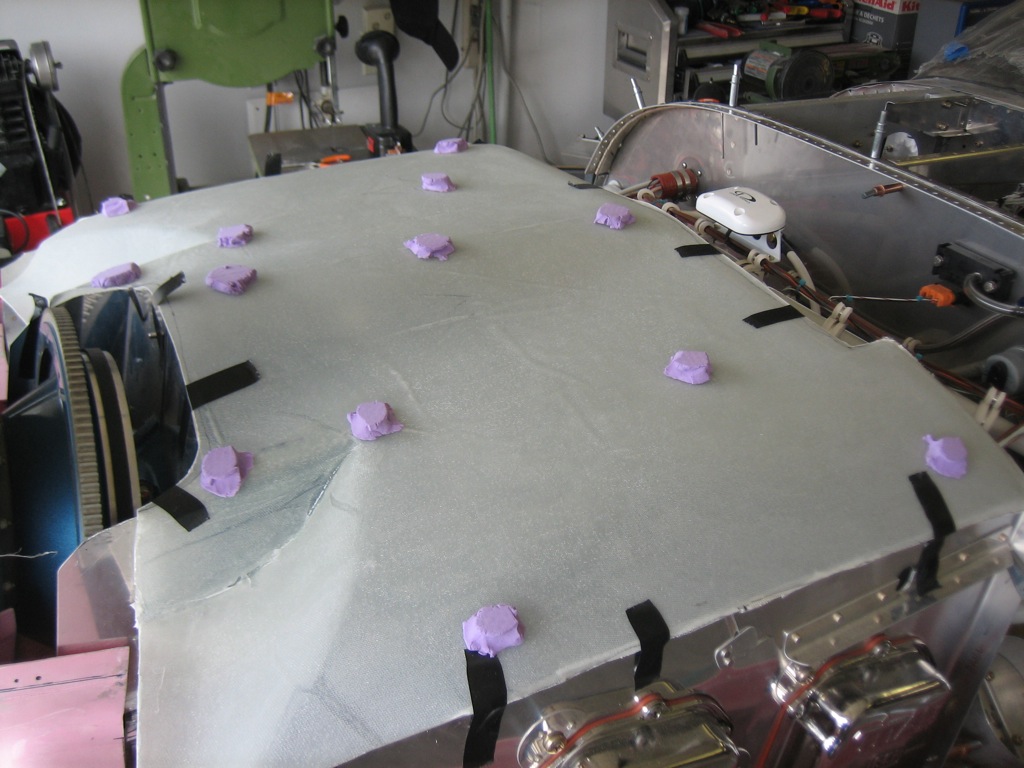